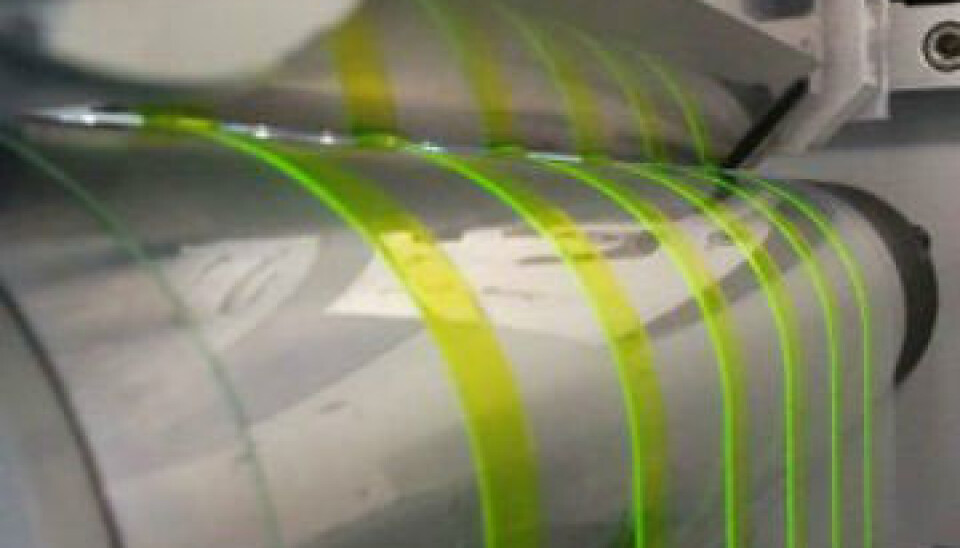
Scientists reinvent light
A new method enables scientists to create large, inexpensive and flexible surfaces that can emit light in the same way as an OLED TV screen. This could result in luminous clothes, glowing wallpaper and even radiant cereal packets.
Genesis 1:3 – And God said, "let there be light,” and there was light.
Now Nordic scientists are invading God’s turf by reinventing light.
Researchers from the Technical University of Denmark (DTU), together with Swedish colleagues, have devised a new and simple method for creating luminous surfaces with LECs (Light-emitting Electrochemical Cells).
The new surfaces are flexible, inexpensive and can be produced in great sizes.
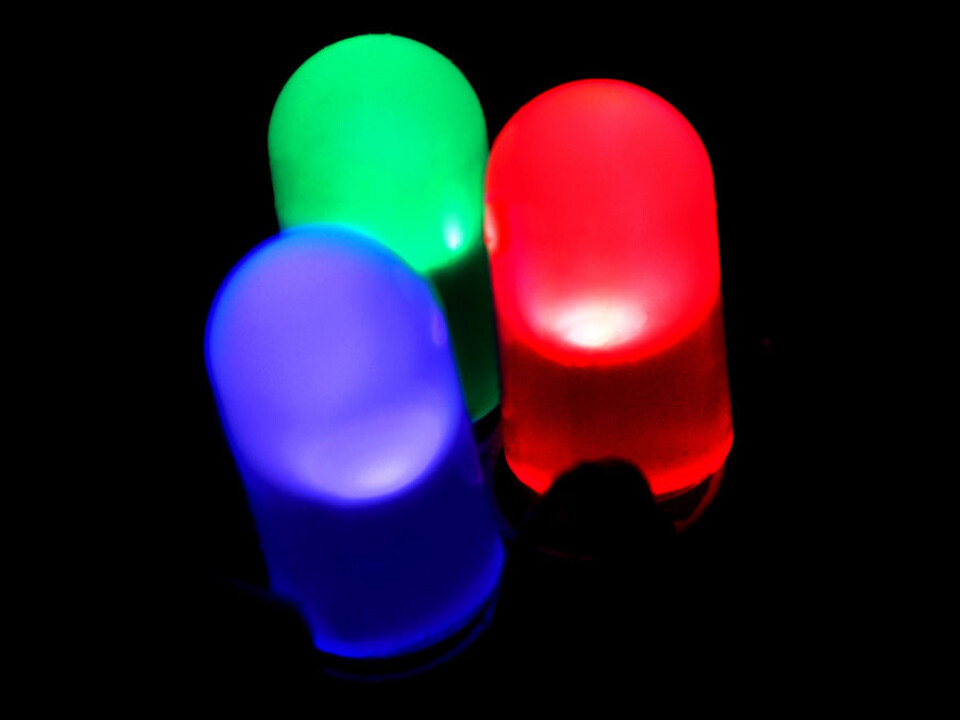
This could revolutionise the future and give light in places we would normally never have thought possible.
“What’s new about our invention is that we can fabricate light-emitting devices using roll-to-roll coating methods, which are similar to the way newspapers are produced,” says Henrik Friis Dam, a PhD student at DTU Energy Conversion, who together with Swedish colleagues invented the new method.
“This makes the production of large light-emitting surfaces cheaper than could ever be achieved with e.g. OLED, which is used in some types of TV screens.”
The invention has been published in the journal Nature Communications.
LEC can make clothes glow
LEC will be replacing OLED in future applications where size and price are important parameters – maybe as early as five to ten years from now.
Henrik Friis Dam
Due to its low production costs and its potentially unlimited size, surfaces with LEC can be used for rethinking the use of light.
The researchers reckon that LECs can for instance be used to make glowing wallpaper and radiant traffic signs.
It’s also conceivable that LECs can be used for making luminous clothing or to light up the inside of e.g. cereal packets, enabling people to see the contents in the dark.
“With LEC, we can create completely new kinds of indoor and outdoor lighting. It’s also cheap and environmentally friendly to manufacture,” says Dam.
LEC overtakes OLED on the inside
It’s long been hoped that the size of OLEDs (Organic Light Emitting Diodes) could be scaled up from television size to something much bigger.
There has been no shortage of attempts to do so, but so far all attempts have failed. The problem with OLEDs is that they are costly and difficult to fabricate.
The materials used for producing OLEDs are sensitive to substances such as air and water, which is why OLEDs invariably depend on the use of one or more time- and energy-consuming process steps under vacuum.
The OLEDs also depend on an extremely controlled and uniform thickness to function.
Against this background, it is natural to replace OLED with something new and less sensitive, say the researchers.
LEC can replace OLED
Unlike OLEDs, LECs are notably less sensitive to thickness, oxygen and water. This means that LECs can be produced relatively easily and cheaply using the same technique used for printing newspapers – the so-called roll-to-roll coating method.
“With the roll-to-roll method, a liquid runs out of a crack down on the material you want to print it on.
This could for instance be a transparent plastic sheet,” says Dam.
“Since LEC screens don’t depend on the thickness in the same way as OLEDs do, much less precision is required in the manufacturing of it.”
Successful trials, but some way yet to go
The researchers have already put their new method to the test, and they have succeeded in creating luminous plastic.
However, with a pixel size of 2 x 2 mm and a unit size of 1 x 4 cm, we shouldn’t expect to see glowing wallpaper in the immediate future.
”I admit that our efficiency is not yet ideal. My Swedish colleagues are continuing to improve the resolution, size and efficiency, but we’ve shown that it’s possible.
“LEC will be replacing OLED in future applications where size and price are important parameters – maybe as early as five to ten years from now,” says Dam.
------------------------------------------
Read the Danish version of this article at videnskab.dk
Translated by: Dann Vinther