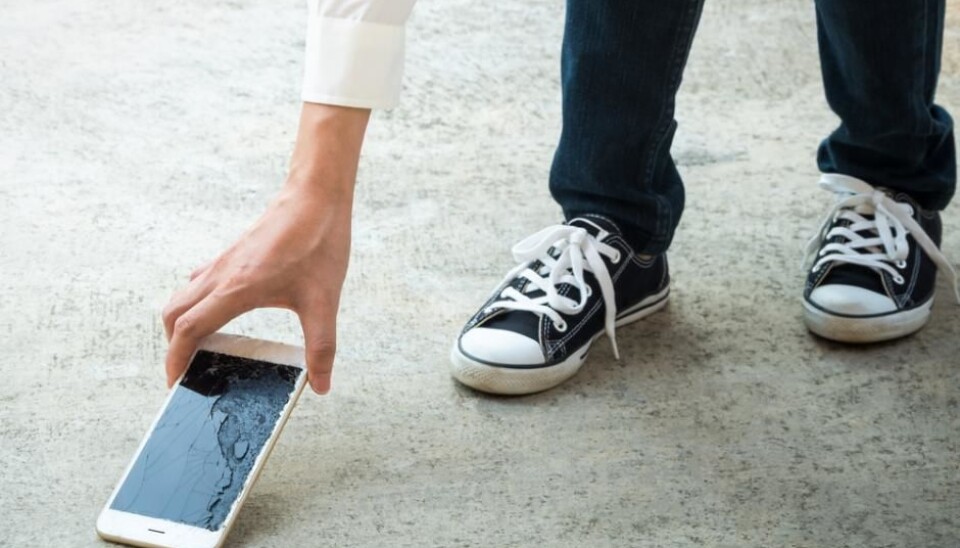
Atomic structure is key to making crack-resistant phone screens
A new material can withstand powerful impacts without breaking and could be used in glass products in the future.
Thousands of years ago, the earliest glass manufactures could never have envisioned using anything other than sand, soda, and lime, to create their glass materials.
But the development of modern technology and the many applications of glass today have put the brittleness of traditional glass to the test. Chips to car windscreens, cracks in smart phone screens, and scratched glasses, are just some of the reasons why scientists continue to study the underlying chemical and physical properties of glass.
As part of a new research project to understand the mechanical properties of this transparent material, scientists at Aalborg University have discovered the most crack-resistant oxide glass ever reported in the scientific literature.
Read More: Swedish glass production 300 years older than historians believed
What makes the new glass so crack-resistant?
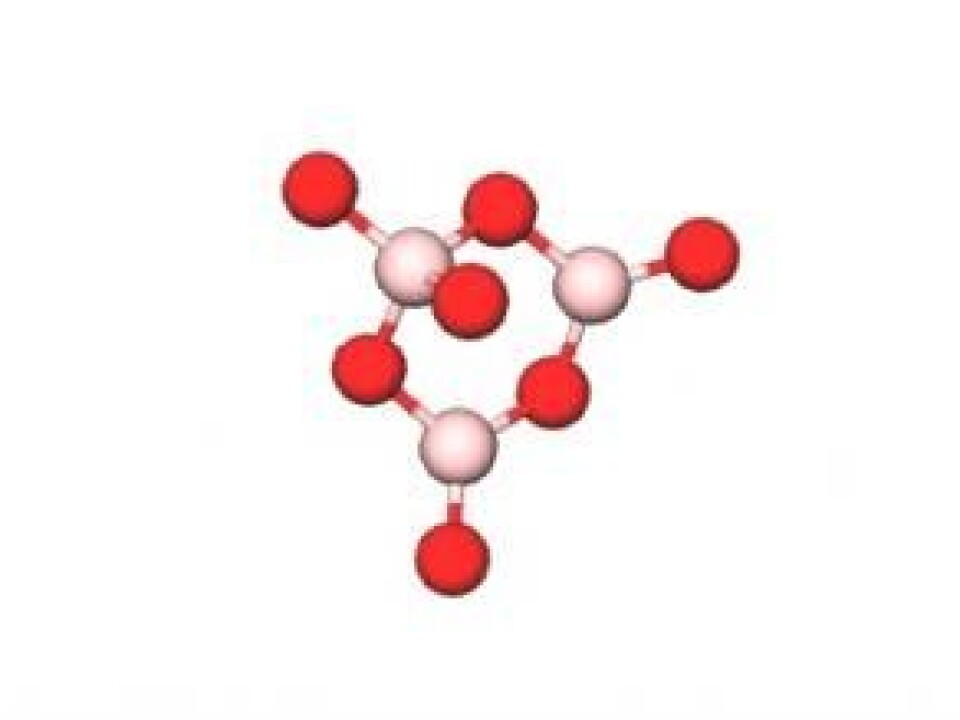
The new glass is made of lithium oxide (Li2O), aluminium oxide (Al2O3), and boron trioxide (B2O3). This chemical composition differs greatly from ordinary window glass, for example, which is primarily comprised of silicon dioxide (SiO2), sodium oxide (Na2O), and calcium oxide (CaO). And it is this new chemical composition that can explain why this new material is so damage resistant.
To understand why, we need to first understand some of the basics of the structure of glass.
SiO2-based glass contains a continuous network of silicon and oxygen atoms, where each Si-atom is chemically bound to four oxygen atoms. But B2O3 is more of a wild card. Depending on the chemical composition, a boron atom can bind to either three or four oxygen atoms.
The atomic structure can also change according to temperature and pressure, which are crucial for glass mechanical properties.
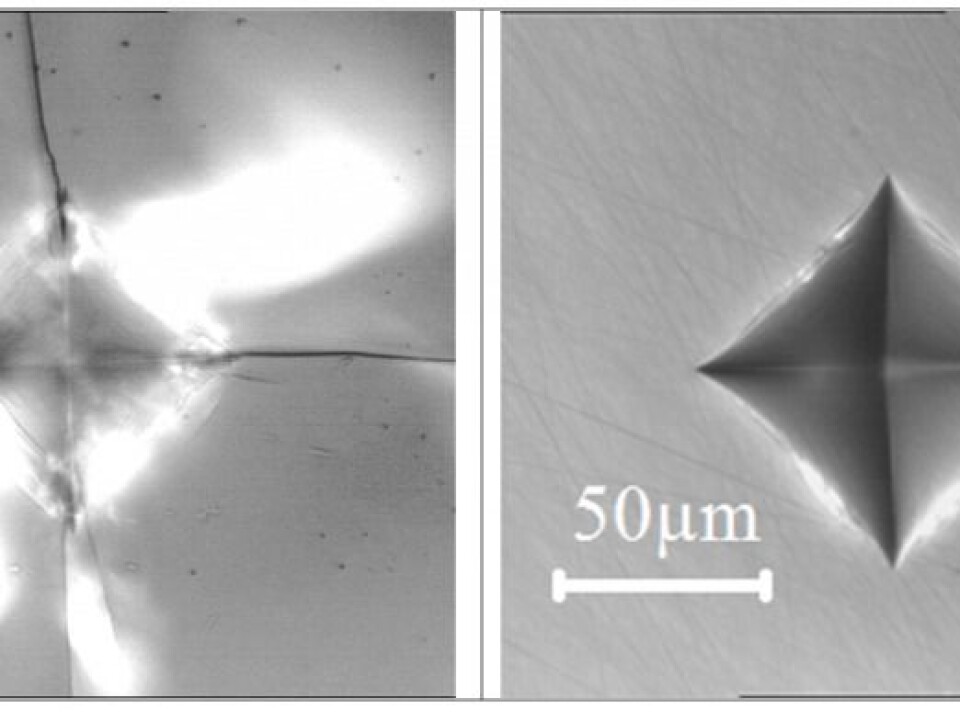
When a glass comes in to contact with another object, for example when a stone chip hits a car windscreen, it creates an area under very high pressure. This can make the coordination number of the boron atom increase from three to four. This ability to change structure would prevent much of the damage to your car windscreen from flying chips on gravel roads.
In this way it creates a permanent change to the glass surface, locally around the site of impact, rather than forming a crack.
Read More: Astronauts test Google Glass on the sea floor
How do we measure crack-resistance?
It can be tricky to measure the mechanical properties of glass since it does not always crack when exposed to a critical load. How many times have you dropped your cell phone onto a hard surface and felt relief when you realise that the screen is fine? But eventually the screen will crack.
Typically we use the hardness test, which allows us to take reproducible measurements in everyday type scenarios. In this test, we use the hardest substance known on Earth, a diamond tip to exert a pre-defined force onto the surface of the glass.
Afterwards, the area is inspected using optical microscopy and the imprint is evaluated in terms of the number of cracks created. The measurements are repeated for a range of different loads so we have a solid statistical basis for our subsequent calculations.
Read More: Scientists get to grips with a tricky liquid
Needed improved equipment
In these tests, we start by applying a relatively low force: Not enough that it cracks, but enough to make a permanent depression in the surface.
The load is then gradually increased and the number of cracks observed is expressed as the probability of cracking. The load is increased until 100 per cent probability of cracking is reached. The challenge with such a procedure is that many of the existing hardness testers for glass are limited by the maximum force that can be exerted, typically between one and two kilograms.
Our old equipment was challenged when evaluating the crack-resistant B2O3-based glass, which is so resistant that the maximum load of two kilograms resulted in just five per cent probability of cracking. So we needed new equipment to measure the crack-resistance of this material.
We invested in a new hardness tester, which offered ten times the load while also enabling measurement of the elastic response of the glass, as well as performing a so-called scratch test, where a diamond tip is moved across the surface.
This gives us a wealth of options to compare a number of different types of glass and advance our knowledge of the basic properties of these materials.
Read More: Making beer bottles from paper
When will the glass hit the market?
But the new material has one practical hiccup, which would eliminate it from use in many everyday applications right now: Over time it goes from shiny to matt after contact with water.
This happens because the B2O3 is more hygroscopic--meaning it reacts with water--than SiO2.
We are now working on possible solutions using other components of glass. For example, a recipe that replaces Li2O with MgO shows promising results.
For now we need to compromise between the mechanical properties and the chemical resistance of glass materials. But the discovery has given us an insight into the structural mechanisms that cause cracks. We expect future research to draw on this and develop new chemical compositions for glass, targeted towards more industrial applications.
---------------
Read this article in Danish on ForskerZonen, at Videnskab.dk
Translated by: Catherine Jex