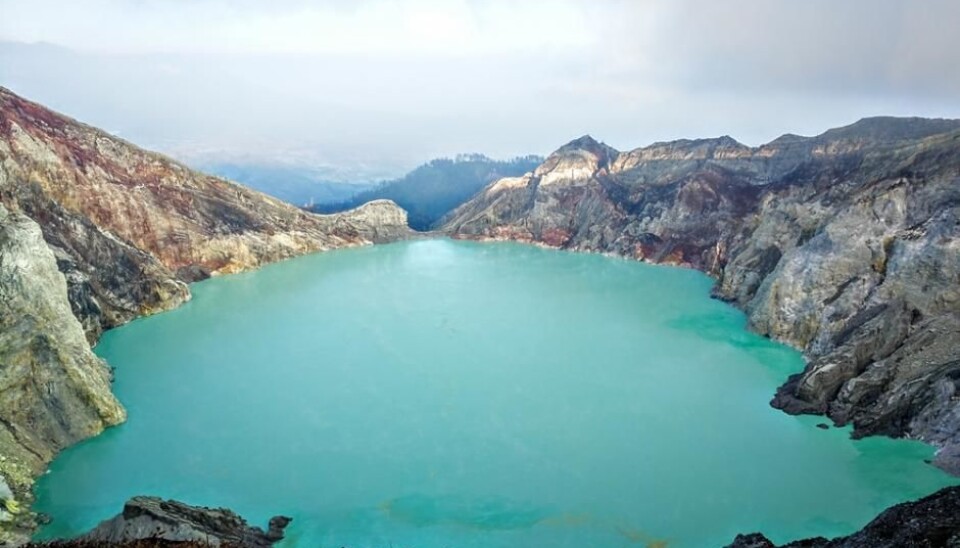
Sulphuric acid was the bedrock of the Industrial Revolution
And it is still used in fertilisers the world over today.
The English man John George Haigh (1909-1949) is famous in criminal history circles as the “acid bath murderer.” Between 1944 and 1949 he killed six people and disposed of their remains by dissolving them in large vats of concentrated sulphuric acid.
Haigh mistakenly thought if there was no body, he could not be convicted of murder. But his perverse use of the corrosive properties of sulphuric acid did not help conceal his crime. On the 10th August, 1949, he died on the gallows.
But sulphuric acid (H2SO4) has many more less gruesome uses, and is in fact the backbone of the modern chemical industry and the most commonly used of all acids.
People have known about the sulphate minerals of iron and copper since ancient times, when they were referred to as vitriol.
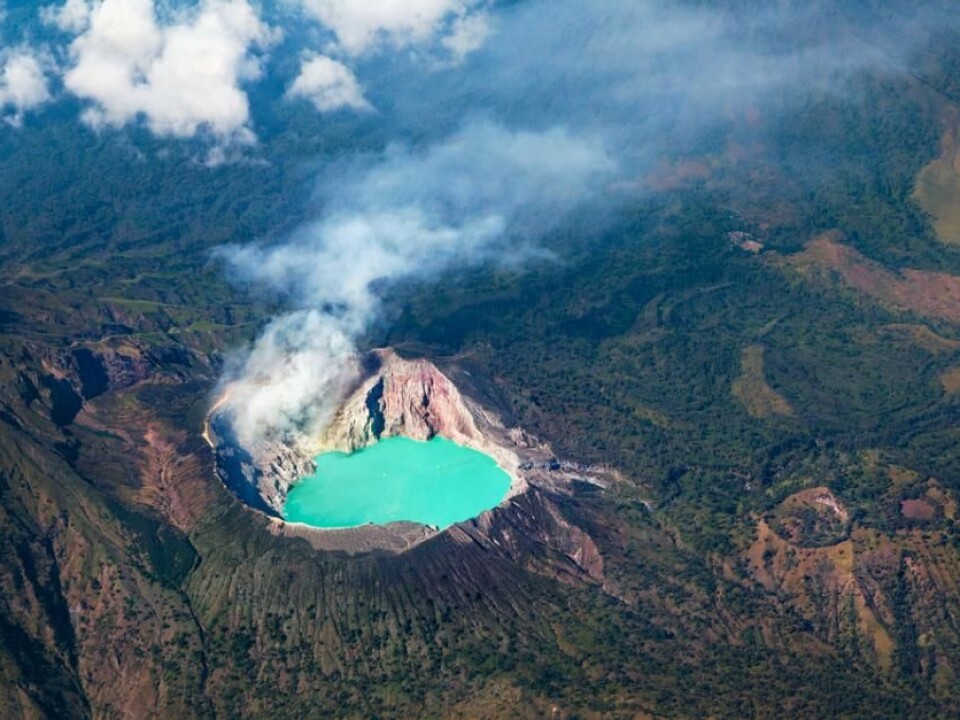
Our ancestors used vitriol for metallurgical and medical purposes, but learnt much later that vitriol could also be used to make strong acid. The discovery is often attributed to the Muslim alchemist Jabir ibn Hayyan (ca. 721 to 815 CE), who became known as Geber and whose writings were known around 1300 CE.
Read More: Medieval copper smelter find is Norway's oldest
Sulphuric acid used to colour clothes
Alchemists in the Middle Ages developed a method combining green vitriol (iron sulphate, FeSO4, 7H2O) with nitre and water over heat in a glass or stone pot. The result was called oil of vitriol due to its oily consistency.
Our language preserves these old connections between vitriol and sulphuric acid: We still refer to vitriolic satire, meaning a biting or corrosive form of comedy.
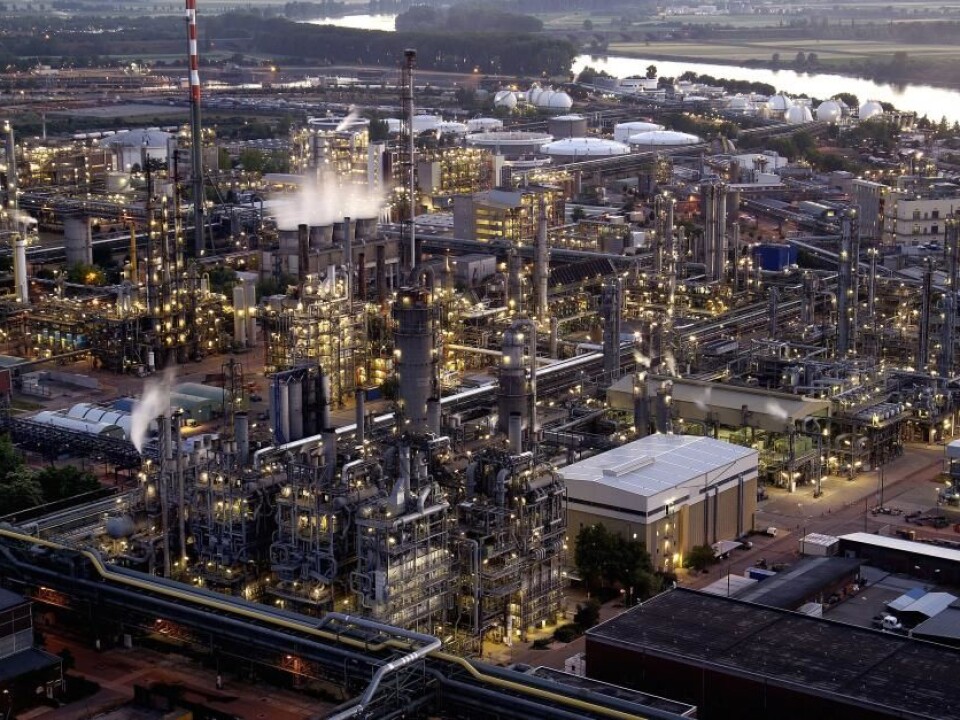
Demand for sulphuric acid remained low until the mid-1700s. Until then it was limited to the production of Glauber's salt or sodium sulphate decahydrate, which was sold in pharmacies as a cleaning agent and named after the German chemist Johann Glauber (1604 to 1670) and is still sold in health shops today.
Production increased from around 1760 when it became used as a fabric dye in place of the traditional bleaching technique using soured milk.
The acid was used to produce a dissolvable form of the blue plant dye, indigo, into a form that could be dissolved in water. As a bleaching agent, sulphuric acid became very quickly replaced by the more effective chlorine, but it did not diminish the importance of sulphuric acid. On the contrary.
Read More: This rock switches colours in an instant
Crucial role in the Industrial Revolution
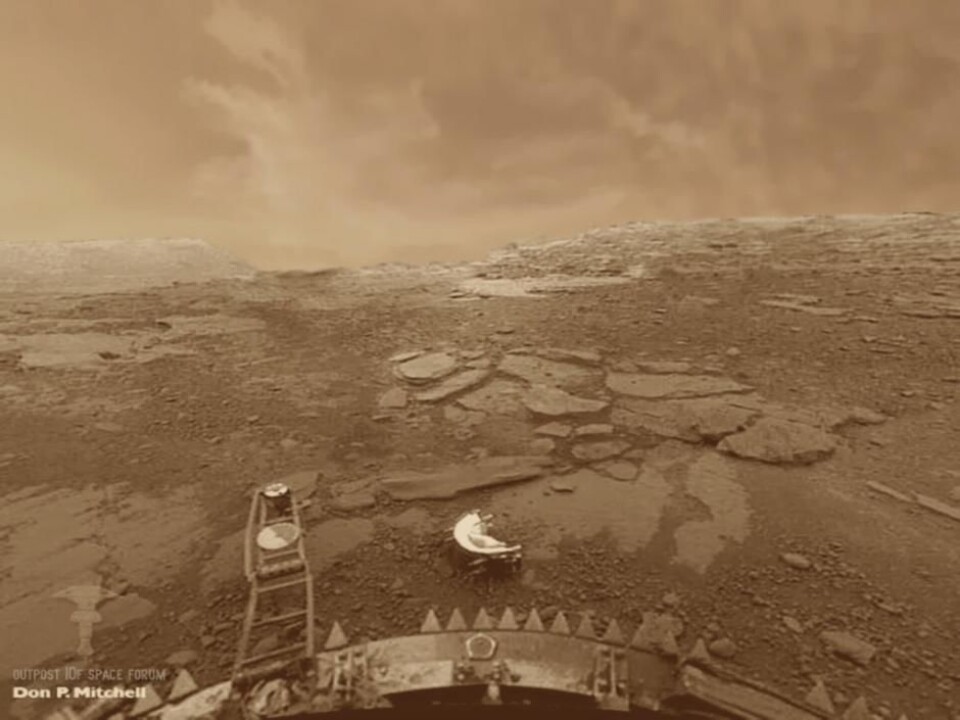
The success of chlorine bleaching resulted in further demand for sulphuric acid. Chlorine is largely made of hydrochloric acid (HCl) by combining sulphuric acid and cooking salt (H2SO4 + 2NaCl → 2HCl + Na2SO4).
The rise in demand led to the so-called lead-chamber process, which dominated the sulphuric acid industry until the beginning of the 20th century.
It was first introduced by the English inventor John Roebuck (1718 to 1794), who was one of the leading figures of the industrial revolution and worked with James Watt (1736 to 1819) to develop the steam engine.
The original version of the lead-chamber process consisted of volcanic sulphur or pyrite (FeS2) combusted in the presence of nitre (KNO3) in large chambers of lead, which is not corroded by sulphuric acid, unlike other metals.
Water or steam is then added gradually to produce sulphuric acid with a concentration of around 60 per cent. This can be further concentrated by heating in platinum kettles.
In chemical terms, the process is summarised as follows:
Sulphur dioxide is created by burning sulphur: S + O2 → SO2.
This is then used to create sulphuric acid: SO2 + O + H2O → H2SO4.
Nitre is used to impart the oxygen atom (O), which converts the sulphur dioxide gas to sulphuric acid. In the 1700s, they probably did not understand the chemical mechanisms behind these reactions, but this did not prevent the progress of the sulphuric acid industry.
Read More: 1,750 skeletons tell stories of life during the industrial revolution
Sulphuric acid production in Denmark
A number of technical developments in the 1800s lead to larger and more effective factories producing acid of up to 80 per cent concentration throughout Europe and North America.
Denmark produced a modest amount of sulphuric acid with the establishment of the Fredens Mølle factory in Amager (south Copenhagen) in 1834, by the British-Danish tradesman Joseph Owen (1789 to 1862).
Sulphuric acid took prominent place in technological and industrial history due to its use in a number of chemical products, including hydrochloric acid, hydrogen, super phosphate, bleach, and soda.
The acid had the same crucial role in the chemical industry that the steam engine had in the mechanical industry, and silica in current information technology.
In his popular book Chemical Letters, the prominent German chemist Justus von Liebig (1803 to 1873) wrote:
“We can accurately assess the chemical industry of a country according to the amount of sulphuric acid it consumes.”
In a parliamentary debate, the British Prime Minister Benjamin Disraeli (1804 to 1881) characterised the production of sulphuric acid as a barometer of a nation’s degree of industrialisation. His own nation was highly industrialised, producing 600,000 tons of sulphuric acid by 1870—more than any other country. Denmark was producing 3,500 tons at the time.
Read More: A third industrial revolution for Norway?
Two tons of sulphuric acid to inflate a balloon
Sulphuric acid even had a role to play in balloon flight. Hydrogen balloons were introduced in 1783 by the French physicist Jacques Charles (1746 to 1823) and his assistant who used a balloon filled with the combustible gas to travel. This gave the balloon the lift it needed to fly.
To produce the hydrogen gas (H2) they used iron fillings doused with large amounts of sulphuric acid (Fe + H2SO4 → FeSO4 + H2). But the large hydrogen balloon required around two tons of sulphuric acid and a corresponding amount of iron, making it an expensive and laborious process.
More important however was the role that sulphuric acid played in the production of the form of super phosphate, which from the middle of the 1800s was used in large quantities as fertiliser.
Naturally occurring mineral phosphates, such as calcium phosphate, are not particularly soluble. It has to be made into soluble acidic phosphate before it can be used as fertiliser on the land. As Liebig showed in 1841, this could be achieved with sulphuric acid.
Liebig’s discovery kick-started a thriving industry, where the mineral phosphate is combined with sulphuric acid. This produces acidic calcium phosphate (CaHPO4), which is soluble in water and can therefore be taken up by plants.
The large demand for super phosphate in European farming resulted in a large demand for sulphuric acid. Today more than half of the global production of sulphuric acid is used to produce super phosphate and other nutrients.
Read More: Little valley – a giant battery?
Growth in demand leads to strong competition
The original sulphuric acid industry was largely based on recipes developed by craftsmen themselves, but by the end of the 19th century chemical research played an important role.
By then, the once dominant lead-chamber process was competing against a new method known as the contact process. By the end of the First World War, the contact process had taken over world markets and most sulphuric acid today is produced in this way.
The new method produced a purer form of sulphuric acid--up to 98 per cent--which was required by new markets for alizarin, indigo, and other synthetic pigments used by the textile industry.
Read More: EU disagreements delay regulation of harmful chemicals
German research took the new technique global
There was one technical hurdle that threatened to sink the profits of a new textile pigment industry.
The problem was solved by a comprehensive research program implemented by the large German industry group BASF (Badische Anilin und Soda Fabrikation) and led by the industrial chemist Rudolf Knietsch (1854 to 1906) in the 1880s.
Under normal circumstances, the combustion products of sulphuric acid, sulphur dioxide (SO2), does not bind with oxygen in the air. But the German chemist showed that it can be achieved by contact with a suitable catalyst, such as platinum or vanadium oxide (V2O5).
This creates sulphur trioxide (SO3), which in turn creates sulphuric acid as it spontaneously reacts with water (SO3 + H2O → H2SO4).
BASF and another German manufacturer, Hoechst, established the first industrial plant based using the contact process in the mid 1890s. And it is no coincidence that these two firms were the world’s largest producers of synthetic colourants. BASF also became the world’s largest producer of sulphuric acid.
Read More: Bad chemistry: Chemical companies fail to comply with EU regulations
Not a household product
Sulphuric acid is probably not a common household product. It is probably best known as battery acid, which together with distilled water is used in car batteries. But this does not change the fact that our society depends on it.
Sulphuric acid is an immeasurably important chemical, but it is not a good idea to come too close. We can be glad that we do not live on Venus, where not only is the surface temperature a searing 470 degrees centigrade, but the atmosphere is formed of carbon dioxide and sulphuric acid.
While the clouds on Earth rain water, Venus rains concentrated sulphuric acid.
---------------
Read this article in English on ForskerZonen, part of Videnskab.dk
Translated by: Catherine Jex