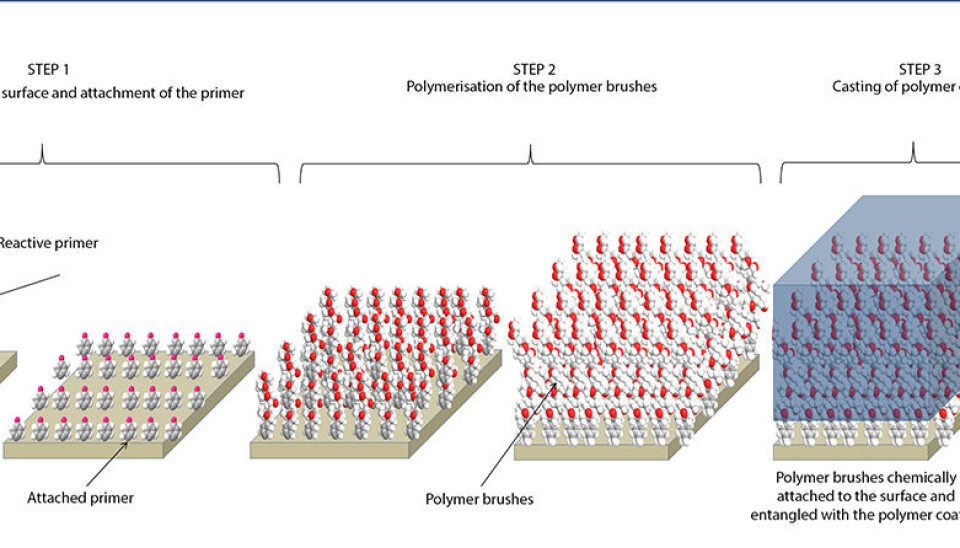
New nanotechnology paves way for molecular super glue
A new method which enables the combination of metals and plastics at a molecular level has been developed by Danish researchers. This ‘molecular glue’ forms strong and tight sealing bonds between materials that would not otherwise stick together.
Many are probably familiar with the problem of paint peeling off metal surfaces due to a lack of adhesion to the metal surface, or where the Teflon layer has lost its grip on the underlying metal on a non-stick frying pan.
The main reason for this so-called delamination is that it is difficult to tie together the different types of materials with sufficiently strong and tight bonds.
These problems have now been addressed by a research group at Aarhus University in collaboration with two local companies, SP Group and Grundfos.
During the past few years the research group has developed a new nanotechnology that optimises on a molecular level the adhesion between plastic and metal.
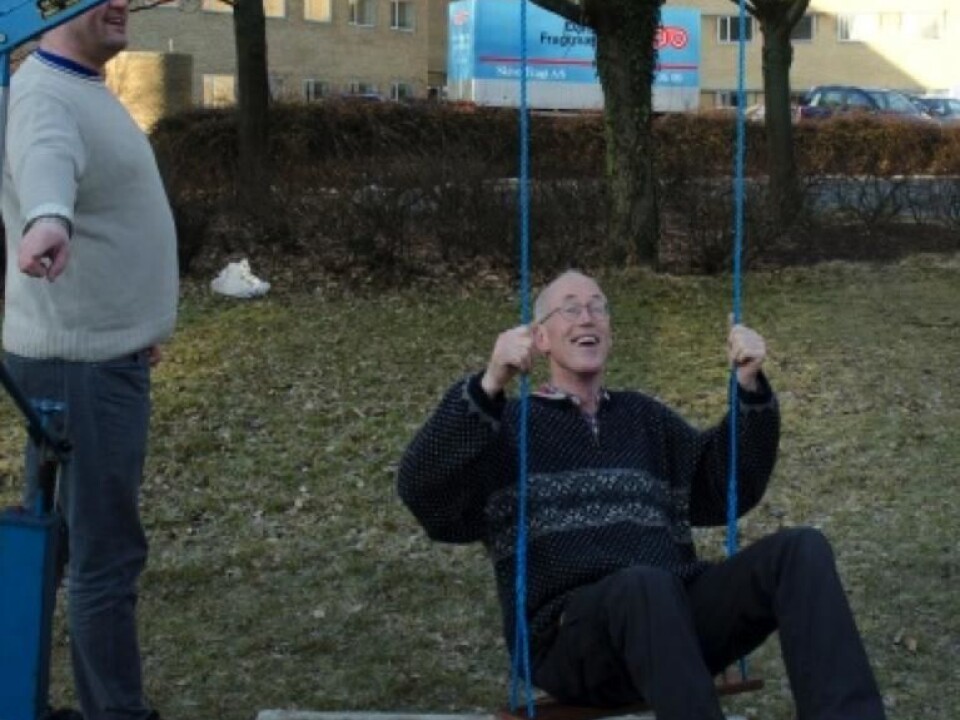
Particular advances have been made in the production of surface-bound polymer brushes applied in the areas of coating technology, smart hybrid materials and polymer composites.
These polymer brush layers are very thin – usually only 30-200 nanometres in thickness. A nanometre is a billionth of a metre, so materials in nano size are invisible to the naked eye.
Surface coatings are good – but they can get even better
Surface coatings and adhesion play a key role in many industrial processes and products. They can protect against rust and other forms of corrosion, reduce friction, repel dirt, increase wear-resistance and make the products look more aesthetically pleasing.
Up to now, however, the use of polymer coatings on a variety of materials has been limited by low adhesion due to a lack of strong chemical bonds to the surface.
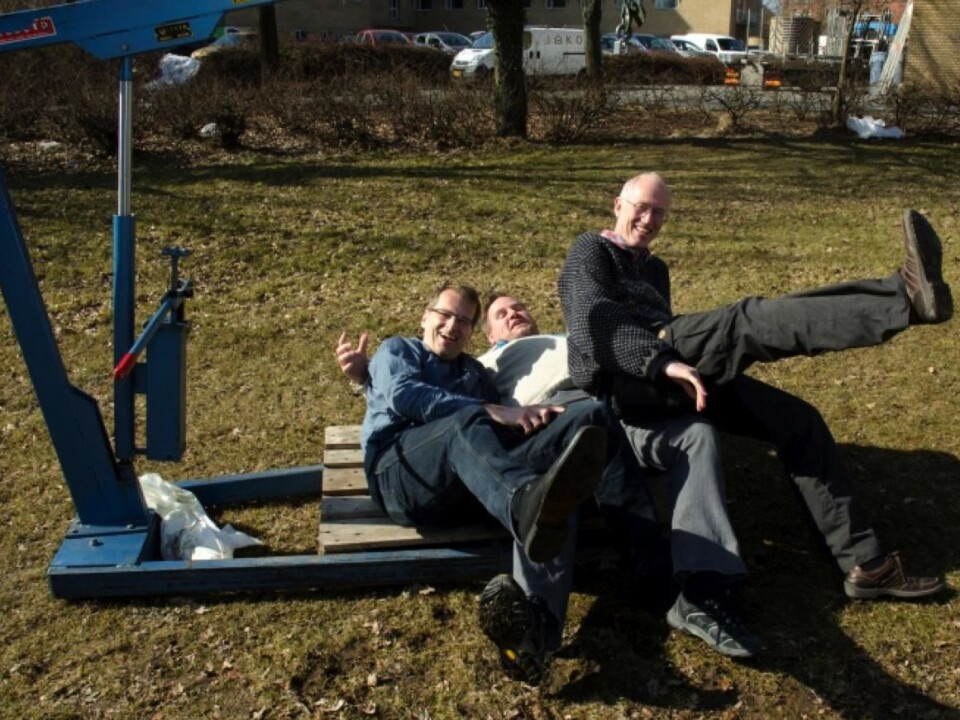
With the new technique it is now possible to modify metal surfaces with specially designed polymer brushes, which ensure extraordinarily strong adhesion between various materials such as stainless steel and Teflon-like polymers.
This reduces the risk of delamination of the applied polymer coating – i.e. that the materials separate – often followed by corrosion, which leaves the industry and society as a whole with massive bills for maintenance, repair and new purchases.
How to apply the molecular glue
The attachment of metal to plastic occurs through a three-step process as illustrated above.
-
In the first step, organic molecules with predetermined functional groups are bound to the metal surface (iron, chrome, steel, etc.) by the combined use of radical chemistry and electrochemistry. These molecules are called primers, or initiators, since they form the starting point for the formation of polymer brushes.
-
By applying well-described polymerisation techniques, polymer brushes can be made in predetermined lengths (typically 30-200 nanometres) and densities. In this part of the process, the researcher’s chemical understanding of polymers is crucial to ensure that just the right properties are built into the brushes, thus making them compatible with the polymer coating to be applied in the following step. For instance, if a coating of poly(methyl methacrylate) – better known under the trademark perspex – is used, brushes consisting of the very same material may be employed.
- In many industrial processes, the polymer coating is applied in molten state, which under the right process conditions enables the polymer brushes to entangle with the polymers in the melt, where they will be captured after cooling down.
In other words, the surface-bound polymer brushes end up acting as a molecular glue, which can make two incompatible materials such as e.g. metal and plastic form strong chemical bonds and stick together.
Competitive on price and quality
Tensile testing has shown that the adhesion between a steel surface and a perspex coating can withstand a weight of around 100 kg per cm2, which meets most industrial requirements.
It is important to keep in mind that the molecular glue has a typical thickness of 80 nanometres, which means that, overall, as little as 0.01 milligrams of glue is used per cm2.
This also means that although the material cost of the molecular glue is considerably higher than for conventional adhesive systems, the technology will still be highly competitive both in terms of price and quality.
The industry wants molecular glue
A molecular integration of materials has good odds of finding industrial applications in the casing of electronics and generally for more effective corrosion protection, thanks to the high durability of the attachments/polymer coatings.
Major industrial players such as LEGO, Kamstrup – a major manufacturer of water meters – and the British company Techflow – a supplier to the oil industry – have teamed up with SP Group, Grundfos and Aarhus University to intensify the development of commercial products based on this new discovery.
Through this partnership, the new super glue will be developed to solve many practical challenges, including protection of oil equipment, encapsulation of electronics and the development of watertight seals.
The Danish scientists are also working on creating a replacement for the widely-used O-ring, which is used for sealing lids, covers, caps and bolt heads.
Next up are smart surfaces based on polymer brushes
The research group at Aarhus University is currently applying for funding for the further development of the next generation of polymer brushes, a generation that will give rise to smart surfaces.
Additional functional groups will be chemically introduced to adjust the properties of the brushes, making them responsive to temperature, light, current pulses, or pH changes.
This would not only significantly speed up the chemical optimisation process; it would also make it possible to join many combinations of metal and plastic, or even plastic and plastic, with the same molecular glue.
In addition, the adhesion can be significantly modified with simple external manipulation and can even be disjoined on demand when the individual components are to be recycled after the product has ceased to function.
--------------------------
Read the Danish version of this article at videnskab.dk
Translated by: Dann Vinther