Researchers' Zone:

How do we make more sustainable concrete that can last over 100 years?
Making concrete sounds easy enough: You mix cement, water, sand and stones and let it harden. But it becomes a lot more complicated to ensure a concrete bridge has a long life.
Do you know how many bridges and tunnels there are in Denmark? Just for the state road network, that is already about 2,500.P
The first large Danish bridges were built in the 1930s: Lillebælt bridge, Storstrøm bridge, Oddesund bridge. These bridges were designed for 75 years of service, meaning that they are getting old nowadays.
For example, the old Storstrøm bridge is in a poor condition and would have required extensive maintenance work in the coming years, if it had not been decided to tear it down.
In recent years, the design lifetime of bridges and tunnels of the Danish Road Directorate has been increased from 75 to 120 years.
In my research, I have tried to find out how to reach this longer lifetime for future bridges but with less carbon-intensive materials.
Building durable structures is not an easy task. Why? Because traffic, rainfall, temperature changes, frost, seawater and de-icing salts are all pretty harsh on construction materials.
However, durability is also key to improving material circularity, by making material loops larger.
This is where my research hopefully can make a difference and help build durable and more sustainable concrete structures.
I just finished my PhD with the Danish Road Directorate and the Technical University of Denmark.
The project was financed by Innovation Fund Denmark and Realdania, and part of the cluster ‘Circular Built Environment’, facilitated by Bloxhub.
Here is what I did, what I found out and why a change to our material regulations might be a good idea.
Durability and sustainability go hand in hand
Bridges and tunnels deal with extremely long lifespans.
Regarding climate impact, the construction phase accounts for a large share of their carbon footprint.
Reducing this impact is extremely important, but durability should not be forgotten.
If a structure is not durable and needs to be repaired or replaced before the planned date, all benefits of a low-carbon design may be lost.
Reducing the carbon footprint of concrete
Traditional concrete is made of Portland cement, water and aggregates – sand and gravel. Among these constituents, Portland cement has the largest CO2-contribution to concrete, around two-thirds of the total.
Most of the time, we add steel bars to concrete to obtain better structural properties. We call it ‘reinforced concrete’.
In this case, steel has a large impact on the carbon footprint too, but Portland cement still accounts for about half the total.
Thus, one of the best ways to reduce the carbon footprint of concrete is to use less Portland cement and replace it with other materials called supplementary cementitious materials, SCMs.
For many years, coal fly ash has been used as the main SCM, for instance for the Storebælt and Øresund bridges.
Coal fly ash is a by-product of coal-fired power plants and is a good example of circularity, where an industrial by-product is reused instead of being left as garbage.
However, since we expect to run out of coal fly ash in the coming years due to the energy transition in Europe, we urgently need to find and use other SCMs.
Selecting the right materials to produce durable concrete is an essential step: As the saying goes, prevention is better than cure.
Choosing the right components for making durable concrete
In my PhD, I tested different SCMs to try to understand how they affect the durability of concrete.
The intention of the project was to develop a generic approach able to evaluate any material. Therefore, I made a selection of materials as diverse as coal fly ash, calcined clays, biomass ashes, sewage sludge ash, crushed brick, or glass beads.
I focused on a specific deterioration process called alkali-silica reaction, which is a chemical reaction occurring between cement-like materials and some aggregates that may end up in severe swelling and cracking of the concrete.
Concrete is a porous material, and its pores are partially filled with a highly alkaline liquid. For concrete made with Portland cement, this typically corresponds to a pH value around 12-13.
Unfortunately, this high-pH liquid is able to attack some aggregates, which is the starting point for alkali-silica reaction.
Alkali-silica reaction is a well-known issue in Denmark because several natural sand deposits contain porous flint, which is a mineral highly unstable in concrete.
It has been a major concern for Danish bridges built in the 1960s and 1970s. Stricter regulations on concrete were enforced in 1987, and no new case of alkali-silica reaction has been reported on structures built after 1987.
However, these regulations were set for traditional components of concrete. Therefore, we must assess if they are still suitable for new types of SCMs.
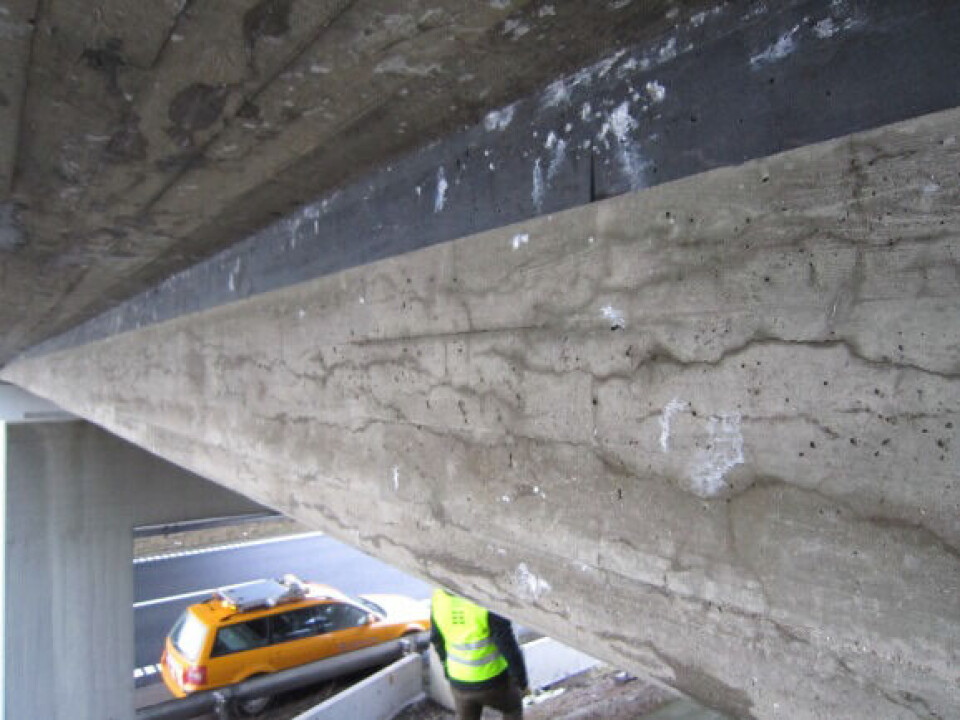
Here’s what I did
Because the alkali-silica reaction may take several years to develop in real concrete structures, we use accelerated laboratory tests to get faster results.
To accelerate the tests, we can for instance increase the temperature or add chemicals to boost the chemical reactions.
I tried different concrete recipes and tested them both in accelerated and real outdoor conditions. I kept track of the length of the specimens over time to detect any expansion, and I inspected the surfaces visually to see if cracks appeared.
In addition to this, I also performed other tests to study the effect of SCMs with a chemistry approach.
This has been done by other researchers previously (see here, here and here), but they used an expensive setup which is only available in a few laboratories around the world. I did these tests on paste samples, i.e. cementitious materials mixed with water – without sand and gravel.
Therefore, my work focused on simplifying the method to make it convenient and applicable outside high-tech laboratories.
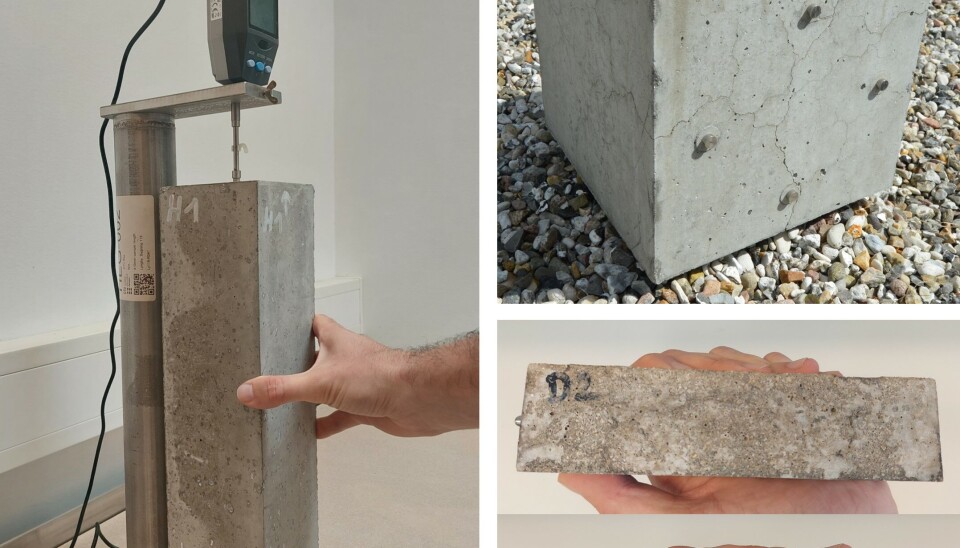

Mixed, but promising results
When analysing the results, expansion tests gave different results between2 the laboratory and outdoors.
One of the reasons is that most expansion tests were initially created to test specifically sand and gravel, not the entire concrete mix.
Therefore, in some cases, the accelerating conditions disturb the chemical reactions involving cement-like materials and distort what occurs in real life. As a result, it can lead to an inaccurate evaluation of the performance of an SCM.
In other words: accelerating the tests should not be done at the expense of reliability.
The simplified chemical tests on paste samples showed that SCMs can modify the pH of the pore liquid.
Some SCMs lowered the pH, which is beneficial to prevent alkali-silica reaction. Essentially, this is what I was hoping to be able to do.
However, a few SCMs had the opposite effect.
Interestingly, the simplified chemical tests matched fairly well with the outdoor concrete exposure blocks: the mixes with low pH did not show any sign of expansion, while the mixes with high pH had clear signs of damage.
This is quite promising because it agrees with the conclusions of other studies (see here, here and here) but with a simpler method.
Moreover, paste specimens are easy to produce and handle, which makes the testing procedure more convenient.
Still a few steps to go before new SCMs are put into practice
You may wonder: Does this mean we can already use new SCMs in real constructions such as bridges and tunnels? Well, not yet.
There are very specific rules to follow when producing concrete, in particular regarding the choice of materials. The main framework is defined at the European level, but each country sets its own acceptance criteria.
At the moment, the regulations cover traditional SCMs fairly well, but are not really suitable for new types of SCMs; updating the regulations could help us use more new materials, for instance by requiring a certain level of performance rather than a certain type of material.
Therefore, as a final outcome of my project, I will propose some leads to update the national concrete regulations based on my research findings.
What else happens next? We need to confirm the link between the pH measured in small paste samples and the expansion behaviour of larger concrete samples.
In addition, even though my tests have been running for more than two years, this is quite short compared to the service life of structures. Thus, we must keep monitoring the experiments to confirm the trends we have seen so far.
In this way, we can ensure that replacing Portland cement with other materials does not threaten concrete durability in the long run.